What You Need to Know About the Building Material Supply Shortage
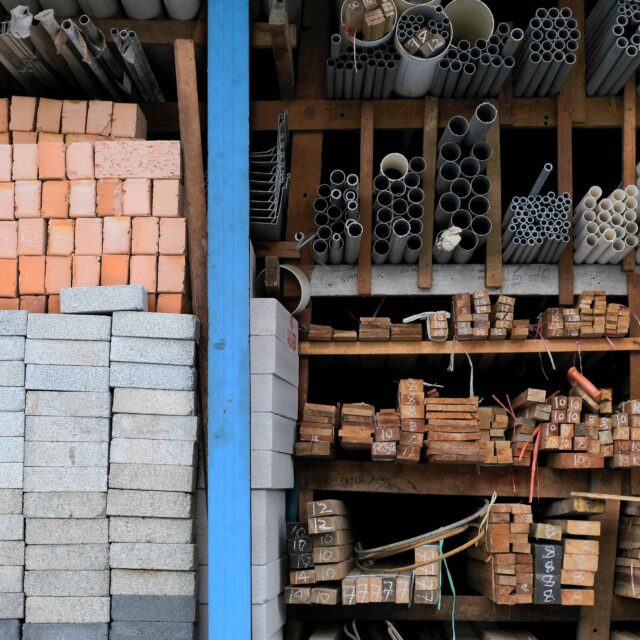
- Written by: jlbmdev
In 2020, most places shut down due to COVID-19. At the time about 75% of companies cited COVID-19-related disruptions in their supply chain and shipping process. Combined with the outside factors that normally disrupt the shipping process, like weather or geopolitical instability, shortages were everywhere, especially in the home and building industry.
However, three years later, is there still a building material supply shortage? In the following blog, we’ll update you on what’s changed in the building industry since our last blog on the topic, and what you can expect when you go to look for building materials.
The main question everyone is asking is “Is there still a shortage of building materials?” The answer is it depends. Some material inventories have stabilized, while others haven’t. So the new question becomes, “What’s the new normal?”
Lumber is essential to the building and construction industry and there was a time when it was in scarce supply. Due to supply chain and manufacturing shortages, you were lucky to even find a piece of wood anywhere, let alone at a reasonable price.
Lumber prices hit a notable high in Spring 2021 when the price of lumber was $1,515 per thousand board feet. Prices pre-pandemic were between $350–$500.
What does lumber look like now? Today you can walk into most building materials suppliers and find what lumber you need for a project, like if you’re building a new deck or adding an addition to your home.
Are lumber prices still high? Yes, but lower than before. They have been coming down over the last year. Now the cost is in the $500 range.
However, could this price go up again depending on the market? Yes, it can. Lumber prices are volatile and dependent on changes in supply and demand. So it’s best to carefully plan out your project and check the market before you commit to building.
Are building materials still hard to find? Most of the time, you can go to a supplier’s showroom and find what you need. Are there still some shortages—yes. There are still issues with the supply chain so you’re bound to have some empty shelves on occasion.
Because of the nature of construction, everything depends on completing the steps that come before it. A delay in one area can push back a timeline for everything else.
For example, there’s a nationwide shortage of electrical transformers. This means any available ones are reserved for emergencies and this delays permits being issued and homes being hooked up to electrical grids. Ultimately you have a completed home but it doesn’t have power so no one can live in it.
One of the items that’s still hard to find is copper. There is a global copper shortage fueled in part by supply chain challenges in South America combined with an increased demand for copper. Some analysts predict that the shortage will last throughout 2023.
Roofing
In 2021, the COVID-19 pandemic affected the roofing materials industry, leading to a shortage of materials. Today the backlogs on roofing materials seem to be decreasing as companies are investing in new technology to help with supply chain issues. However, this can easily be disrupted by outside factors like weather or internal manufacturing issues. Experts are estimating a higher demand for roofing materials for the rest of 2023 into 2024.
Another area where experts are projecting growth is siding. The raw cost of siding is expected to increase along with the demand so the pricing will go up. However, you should be able to walk into a supplier to find siding in stock.
Gutters have always been a competitive market with its own challenges. Due to tariffs on steel and aluminum, the prices for gutters have increased. The good news is that since gutters are usually part of larger roofing projects, those costs can be absorbed into the project’s budget.
Most companies projected a decrease in demand when the pandemic happened and most were surprised when people decided to start home improvement projects. Skylights were no exception.
For example, VELUX expected a dropoff in demand for skylights during the pandemic. As it turns out, the demand increased and they had to adjust their processes to try and meet that demand.
Today skylights follow most building materials in that they’re available but still subject to supply chain issues.
Building material prices have been decreasing since record highs in 2020, but they’re still higher than before. This is partly due to inflation, which will be a continuing issue for the industry. So while it seems like prices are coming down, they’re actually higher than before the pandemic.
It looks like this trend is likely going to be permanent according to an Oxford Economics report due to the increased demand for materials and decreased supply.
With all the delays from COVID-19, construction on new homes was put behind schedule and has been playing catch-up ever since. Add in the building material supply shortage and that gives you a nightmare for people looking to build a new home and for construction companies looking to get back to work.
If you decide to move ahead with your project, what can you do to make it easier? Here are our best tips to help keep your project going smoothly.
1. Place Any Orders As Soon As Possible
Backups can cause materials to be delayed by weeks or even months so it’s best to order your materials early in the project. The earlier you order, the better your chances are of receiving materials by the time you’re ready for them.
2. Do Your Research
With long lead times, the last thing you want to do is need to reorder materials because you measured incorrectly or changed your mind about what material you want. Make sure you know exactly what you need before you order your materials.
3. Don’t Start Your Project Until the Materials Arrive
While it might seem obvious to not start until everything is in, the thought of getting started can be tempting. Especially demolition. However, some renovation projects are more disruptive to everyday life than others.
4. Be Flexible
Be able to adjust your plan accordingly. You may need to revise your schedule, budget, or what materials you use, depending on the severity of the material shortage. If there’s a material you want on backorder, you’ll need to decide if it’s worth it to wait or to find a new product.
After reading all of that, you might be wondering if you should start any home improvement projects. The answer depends on you. While there’s some instability in the building materials market, that shouldn’t mean you should stop your project. Do your research, see what things look like, and carefully plan your project.
There are many details to think about when you’re building or renovating your home. And if one of those details is off, it can derail your whole project.
By working with J&L Building Materials, you have access to our experts who can help guide you through the whole process and help you plan around any building material supply shortage issues. That helps give you the confidence to start your project and help make your home exactly what you want.